3D printing… safe to say that we’ve come a long way. Looking back, this technology is positively space age – it’s revolutionized the medical world, providing 3D printed ears, bones, and even stem cells.
On the catwalks of Paris Fashion Week, we’ve seen 3D shoes rocked by sashaying models, and people have even been making sweet music with printable instruments – case and print made by Designer Scott Summit’s acoustic guitar.
Now? Formula One racing cars are being partly powered by 3D printed components, with McLaren Racing showcasing just what this technology can do out on the race track.
Already improving the performance of McLaren’s line-up are four core 3D printed components – let’s take a look at what they are, and why 3D printing has proven an irresistible technology for this forward-thinking team of racing engineers.
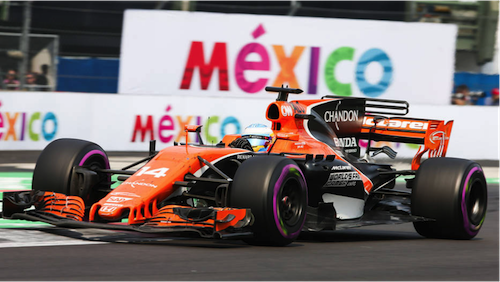
Here are Four 3D Printed Components To Improve Formula One Performance in 2017
1. Hydraulic Line Bracket – Faster, Smarter.
McLaren Honda has created 3D printed structural brackets which attach the hydraulic line on the MCL32 racing car. Harnessing Stratasys FDM technology, the component is rapidly printed off using a Fortus 450mc Production 3D Printer, and is printed using a tough, robust carbon-fibre reinforced nylon (officially known as FDM® Nylon 12CF). As for the time line? Well that’d be just four hours from start to finish, as compared to the traditional manufacturing method which used to demand a full two weeks.
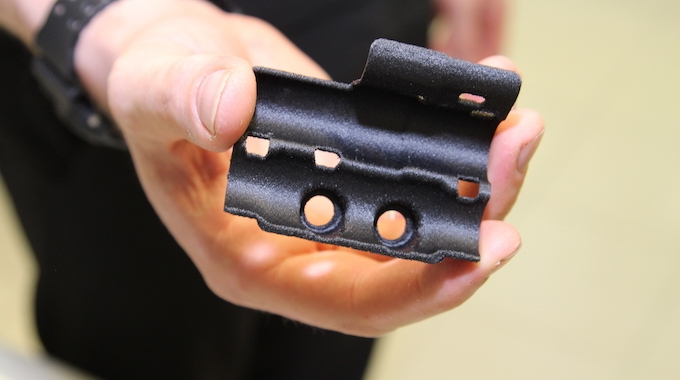
2. Flexible Radio Harness Location Boot – A Perfect Partner For Innovation
Innovation… sometimes with the largest of leaps to improve the performance of a car, comes unforeseen issues that pop up to hold advancement back. This applied to the brand-new 2-way communication and data system that was transforming the communication between driver and car. Whilst the system worked as it was meant to, the necessary cable was proving a distraction to the driver. The solution? 3D printing – to create a flexible rubber-like boot which connected the wires to the new communication system. This component was made possible by the Stratasys J750 3D Printer, and its ability to print off components using pliable materials.
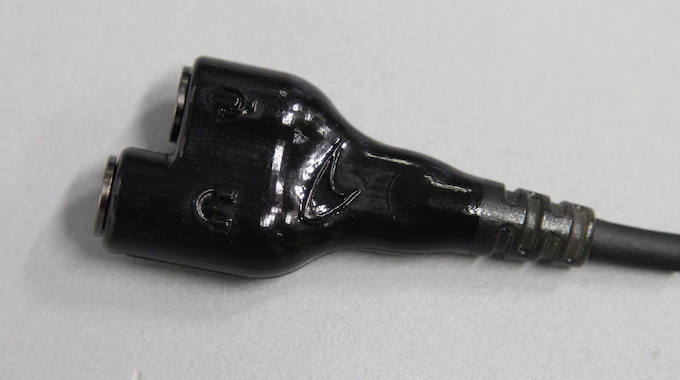
Staggeringly, the development of this component took just one day, with designers creating three different trial designs. The final component was then completed within just two days, easily ready for the road in time for the first 2017 Grand Prix.
3. Carbon Fibre Composite Brake Cooling Ducts
When travelling at speeds of over 200 miles per hour, the brake discs of Formula One cars heat up to extreme temperatures, rapidly. The need for an efficient cooling system is paramount – and it’s this challenge that has also been taken to task by revolutionary 3D printed components. Coming in the form of hollow composite brake cooling ducts, the cores were created using a ST-130 soluble material, which was then encased in carbon-fibre reinforced composite material. Following this the components were then autoclave-cured at elevated temperatures. This created a tube that was super smooth, allowing for optimal airflow to the brakes, as well as maximum aerodynamic performance.

4. Rear Wing Spoiler
A critical component for the aerodynamics of a Formula One racing car, and its ability to stick, steadfastly, to the roads, is the rear wing spoiler. Controlling rear downforce, this component had traditionally been created from carbon-fibre, something 3D printing has been more than capable of handling, heating the materials to over 350°F (177°C) and delivering the structure in only three days (an essential time saver during the mission-critical testing period).
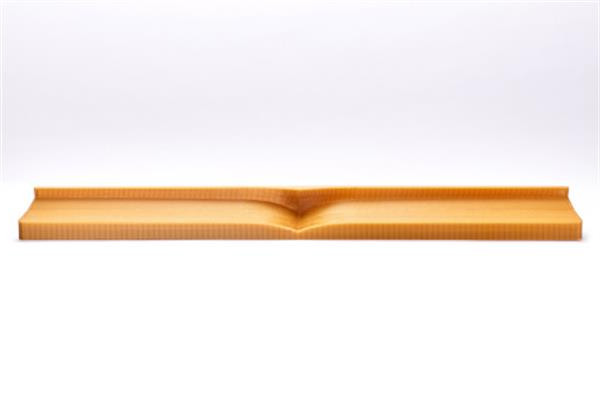
Here’s what Neil Oatley, Design and Development Director for McLaren Racing has to say about it:
“We are consistently modifying and improving our Formula 1 car designs, so the ability to test new designs quickly is critical to making the car lighter and more importantly increasing the number of tangible iterations in improved car performance. If we can bring new developments to the car one race earlier – going from new idea to new part in only a few days – this will be a key factor in making the McLaren MCL32 more competitive. By expanding the use of Stratasys 3D printing in our manufacturing processes, including producing final car components, composite lay-up and sacrificial tools, cutting jigs, and more, we are decreasing our lead times while increasing part complexity”
Neil Oatley
Conclusion
We’re seeing the first, flagship components making their way into the high-performance racing cars of Formula One. As for tomorrow, the possibilities are boundless, as the skilled team at McLaren are taking their Stratasys uPrint SE Plus out on the track to create both parts and tooling on-demand.
There is no doubt that if this does provide a competitive edge then it is merely a matter of time before competing teams follow suit… nonetheless, it shows how forward and innovating thinking keeps you ahead of the game, even if it is for a short period of time.
What are your thoughts? Let us know in the comments. This is a guest article to 3DENGR. Contact us if you have an article you might like to write on a topic for our community.